
Fibre projects
bioluma install - chh wood products
The Challenge
A Bay of Plenty sawmill relied on a wood-processing scanner to seek out defects in their two-by-fours. The machinery told the next piece of equipment which saw to drop, so it could cut away the imperfect section of wood. The scanner was critical to maintaining the quality of their product, and the original tool just wasn’t cutting it.
Our Solution
We worked closely with the client to install a brand new Biolouma scanner. Hutec’s designer spent months based at the sawmill, planning the updated equipment around the original foundations, and successfully tying the old and the new together. The sawmill had a strict shut period of four days to complete the entire install. Just a day over schedule, and the whole project would have had to be put off until Christmas. We pulled together a plan, pulled up our sleeves, and pulled out all the stops to get the job done. We made all the modifications and finished the install within the four day shut. The new scanner regularly cracks 1000 cubic meters of wood a day, making sure each and every one comes out top quality.
3D modelling of complete processing line to determine new equipment and modifications required to fit new equipment and streamline the install process
1000 hours of install effort condensed into 4 days
Dozens of parts manufactured, including shafts, rolls, tensioning equipment, sprockets, chutes and complete end docking saw assembly
End to end process managed, designed, constructed and resourced by Hutec Engineering
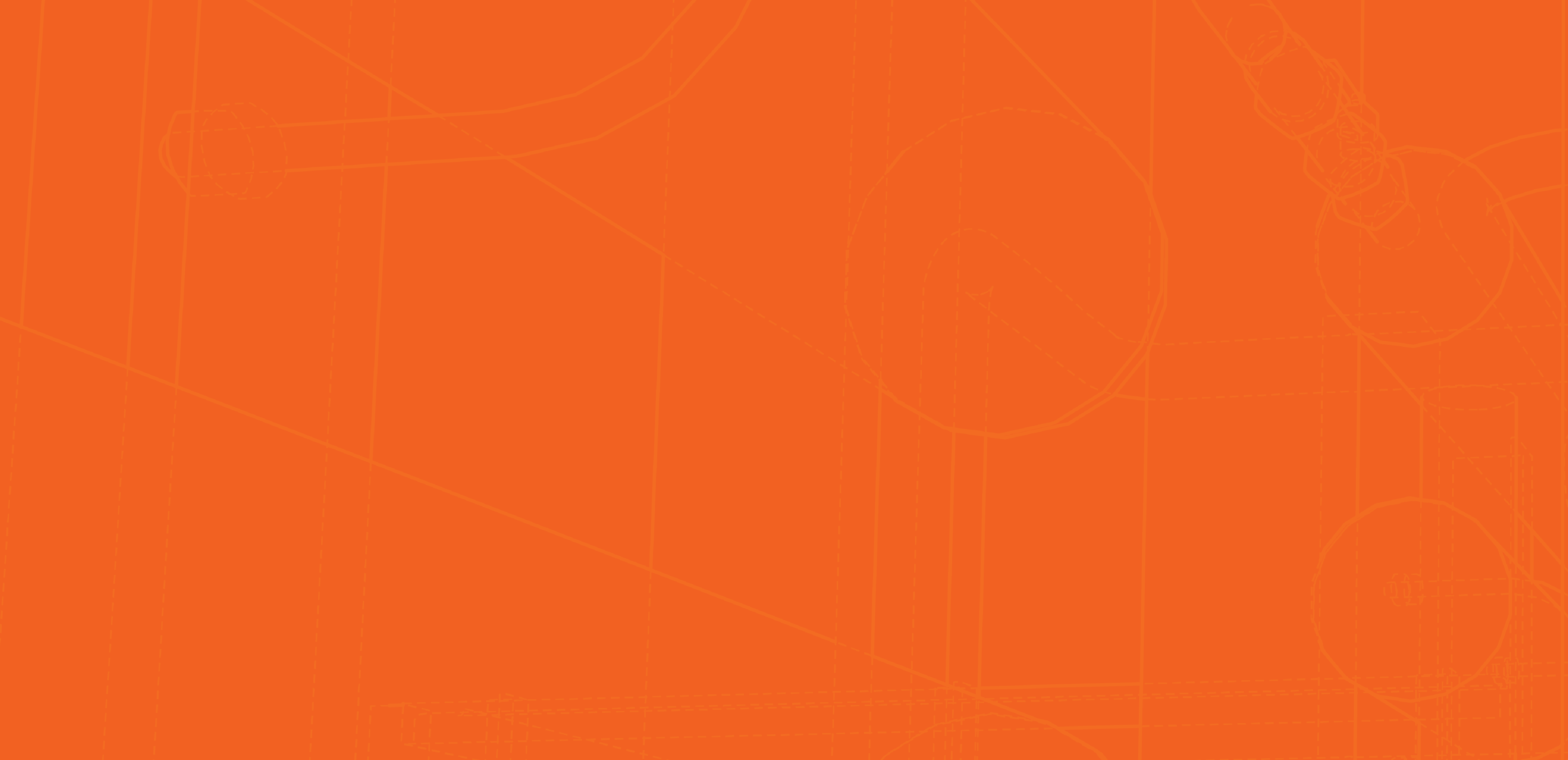
PULP ROLLS - 2021
The Challenge
A forest products company based in Napier used a number of large rolls to control the thickness of their pulp product. The job called for a high level of precision, and their original rolls weren’t quite reaching it. The company had spent years looking for a better solution, and they found one with Hutec.
Our Solution
We engineered a new way to fit the stainless steel-covered rolls to their carbon steel shells. At 6.5-tons each, the rolls are incredibly large – but they rely on just a hair’s width of precision. So our process controlled the fit down to the nth degree, leaving just 1.5mm clearance around the rolls when they were heated to 200°C. The new equipment had improved accuracy and extra longevity. It was the level of technical engineering the client had been looking for. The project’s success saw the scope grow from three rolls to five, and has led to even more work in the pipeline.
SLAB PRESS REFURB - 2020
The Challenge
A Napier-based forest products company used a slab press machine to press their pulp into 600mm2 blocks. The company’s existing equipment was out of date, out of alignment, and badly in need of a refurb. With every cycle, new damage was occurring – to the point where the machine would soon be irreparable. Hutec stepped in with the solution.
Our Solution
We brought in specialist on-site machining tools from Australia, which let us machine the slab press’s surfaces to within .0 of a millimetre alignment. As a one-stop-shop, we were able to work both on-site and in our own workshop – sending multiple parts away for an overhaul, while we held down the fort on-site. We carried out welding, crack-testing, repairs, on-site machining, 3D scanning, and laser alignment. By the end of the project, we got the two 400-ton and 1000-ton hydraulic rams working together in perfect alignment. The clients were thrilled with the result. So much so, they awarded Hutec another large-scale project soon after completion.
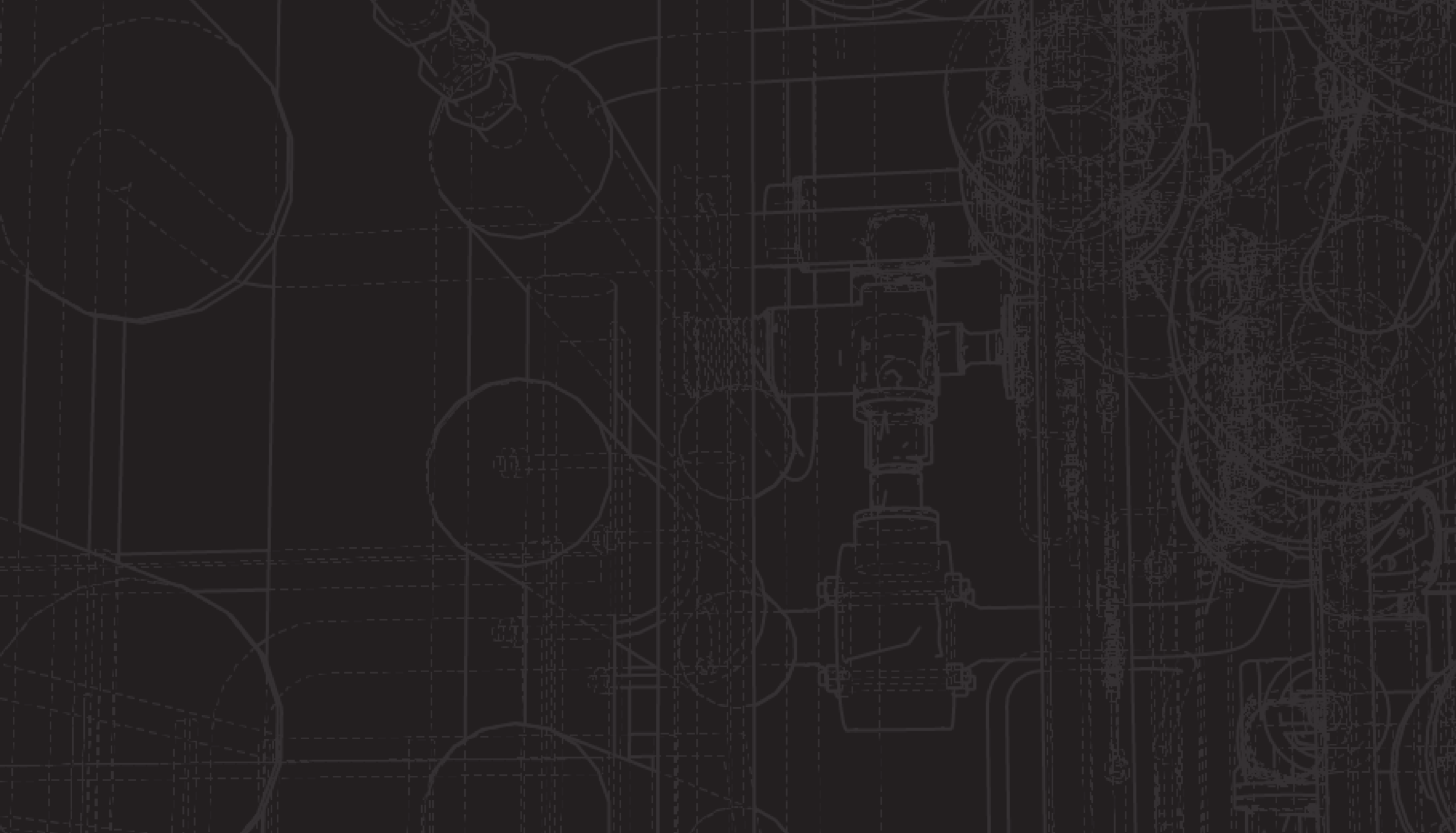
IN-FEED CONVEYOR - 2015
The Challenge
A North Island sawmill used an in-feed conveyor to de-bark a high volume of logs. Their existing conveyor had fallen into a state of major disrepair, with the team spending almost every weekend welding up cracks and carrying out maintenance. They came to Hutec looking for a new piece of machinery that would go the distance.
Our Solution
We took care of the design, build, and install of a brand new in-feed conveyor. Our end-to-end process kept life simple for the client – giving them just one port of call for every stage of the project. We designed the machinery around the sawmill’s existing equipment, and worked with the clients to make sure the foundations were laid just right. For the install, timing was everything. There was a strict shut period of just two weeks, but the foundations had to be laid three weeks prior to being loaded. Making the timing work took precision-level planning. We got it all lined up, and got the project finished to deadline.