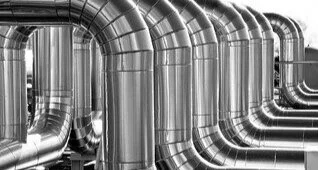
Energy Projects
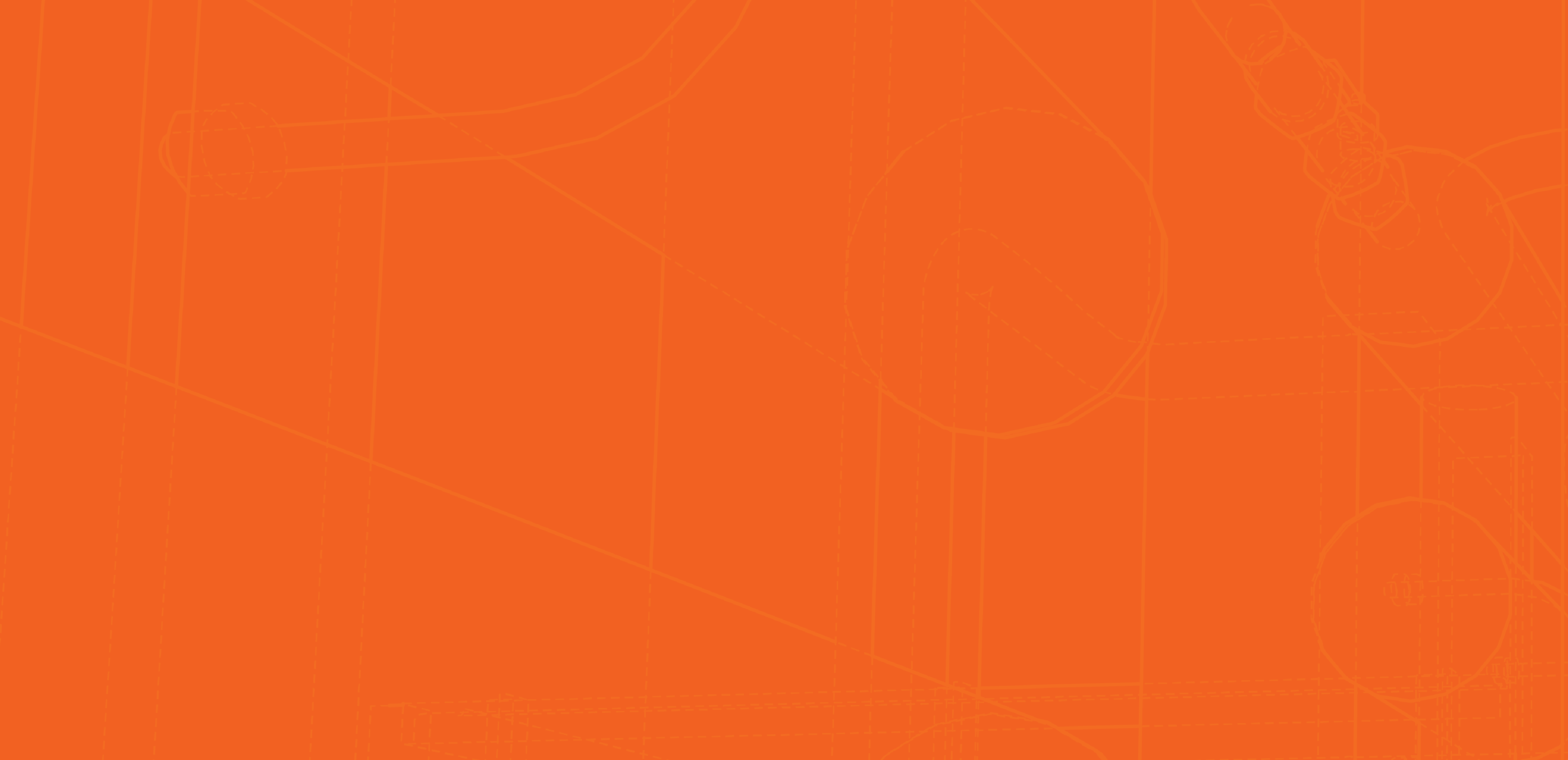
ka57 Pipeline
The Challenge
A Kawerau-based geothermal energy business came to us for help fabricating and installing a steam power pipeline. The client was looking for a partner they already knew and trusted. Having worked with Hutec before, they knew we were the right team for the job.
Our Solution
We partnered with the client to install more than 1.5km of 900mm piping. Shifting each 12m-long, 3.5-ton piece over several road crossings and a state highway was a master-class in logistics. So was the pipeline’s riverside location, which meant dealing with erosion issues, and navigating heavy machinery around waterways. Geothermal pipelines need to withstand high temperatures and high pressures. Quality is paramount, and we were able to assure that quality every step of the way. The pipeline went through the ultimate test when it was filled with over 1 million litres of pressurised water. It passed with flying colours, and not a single leak in sight.
Hutec were able provide an innovative solution that reduced timelines and saved costs, from pre-fabrication of anchor sections in our workshop before installation onsite to transport and installation of large pre-spooled pipe sections.
HOT WELL PUMPS - 2020
The Challenge
While carrying out a regular inspection of a North Island geothermal power station’s hot well pump, we noticed it was in need of attention. Regular water exposure was eroding the stainless steel, geothermal deposits were building up, and cavitation was occuring. The machinery needed new shafts, total realignment – the whole kit and kaboodle.
Our Solution
Hutec carried out a full overhaul – changing out the impellers, installing new shafts, and aligning the machinery. Machining for the project was completed off-site, and transporting the huge and heavy shafts to and from the power station was a logistical feat. We built multiple levels of scaffolding to scale the 5m-tall top of the shaft, and reach down into its basement-level bottom. Stripping away all the old, we brought in the new – including brand new impellers, running with accurate clearances. The finished product was a more efficient piece of machinery, with a much longer life ahead of it.
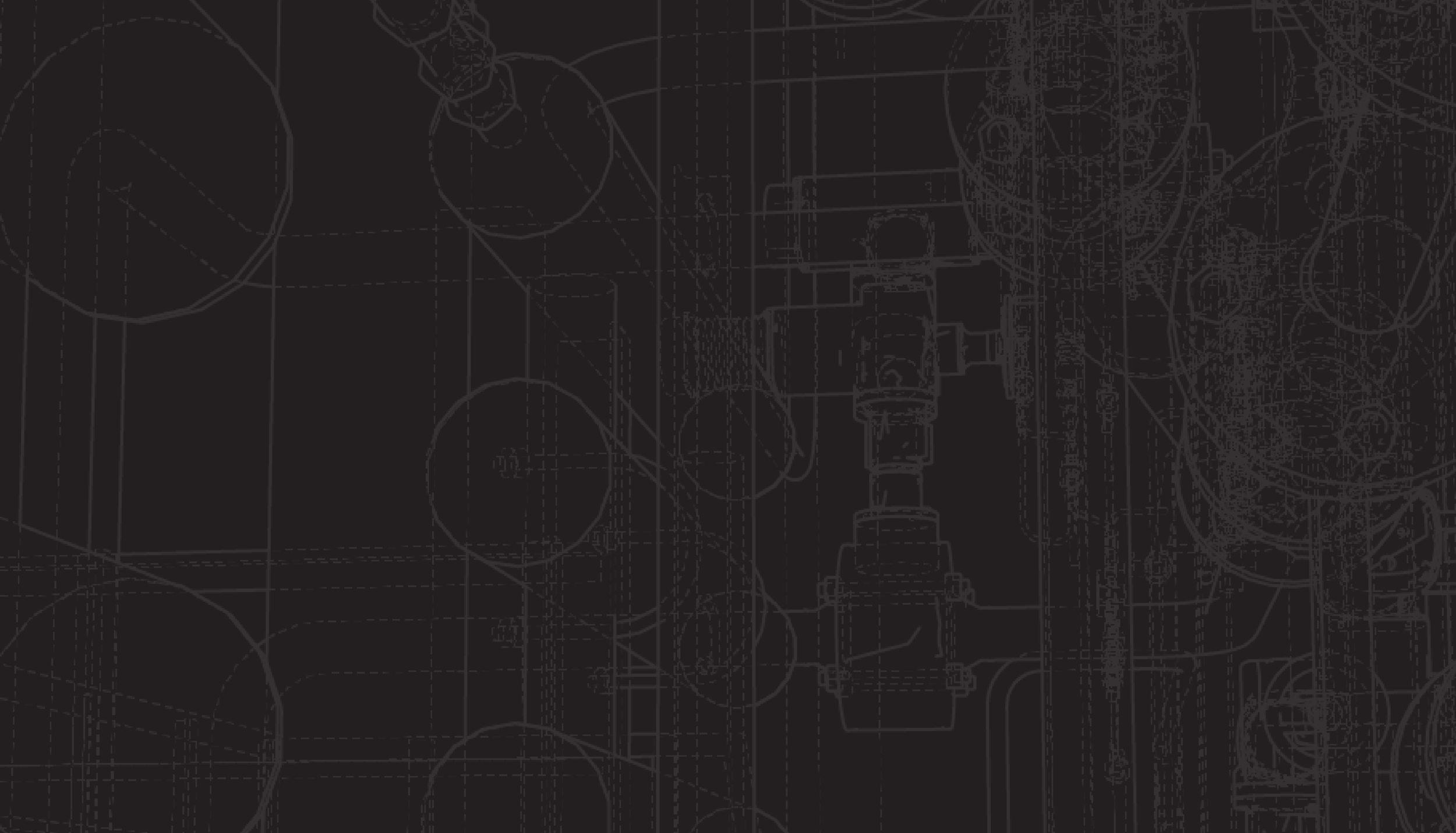
TIMBER TURBINE - 2015
The Challenge
A sawmill based in Rotorua relied on low-pressure steam to run their remanufacturing plant. Their turbine was a critical part of the process – to the point where if the turbine was down, the business would be at a stand-still. Hutec stepped in to make sure the machinery was up to the task.
Our Solution
We carried out the necessary inspections and repairs on the sawmill’s turbine, all during the tight timeline of the company’s Christmas shut. With a manual rigging set-up, we pulled the generator out through the roof of the mill, and performed the overhaul off-site. While standard turbines run at around 3,000rpm, this one ran at 13,000. The high speeds meant close clearances, smaller units, and tighter tolerances – so precision was absolutely key. There was significant erosion in the gearbox, too, which called for specialist on-site machining. This was one of Hutec’s very first major local projects – and the first in a very long list of successes.